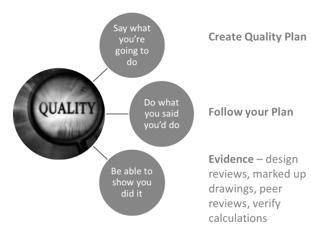
The essence of quality management can be boiled down to three simple concepts: say what you’re going to do, do what you said you would do and be able to show you did it.
Thus, the best way to eliminate quality problems is to minimize the chance of making mistakes with good planning, adequate preparation, and the necessary support. Here are five ways to achieve the level of quality you want and need.
1. Know your team. To overcome the quality problems often associated with a less-than-perfect project team, the PM should review each individual, and identify his or her strengths and weaknesses, then use these traits to the project’s best advantage. Example: You recognize early that the lead mechanical designer is not a strong performer. To ensure that his work will be of acceptable quality (and will be done on time), you provide him with help from the start. On the other hand, the lead electrical engineer has proven herself exceptionally capable. Consider assigning her the coordination of all interfaces between electrical and mechanical, thus ensuring that no major conflicts result in this key area.
2. Plan the work in a logical sequence. Every project has a natural sequence of activities that leads to the greatest efficiency and quality on the job. Deviations from this natural sequence introduce errors that cost time and money to correct. After determining the natural sequence of activities, the PM can estimate more easily the impact of design changes throughout the project. Changes can be made at relatively low cost during the early stages of a project; once the production effort is in full swing. However, every minor change potentially generates many costly errors.
3. Anticipate problems. At the end of each project meeting, spend 10 minutes and ask your team members the following question: “What can go wrong that will hurt the quality of this project?”
List all the responses on a note pad and ask for ideas that can prevent these problems or mitigate their impact. Distribute this list to everyone on the team, especially to those who did not attend the meeting. Keep these lists in the project files and refer to them prior to project reviews with your management and the client.
4. Stay close to the work. Purposely visit with everyone on the team at least once a day to monitor progress and outstanding issues (given geographic and project size constraints). This is especially important for drafters, designers, and specification writers generating the drawings and specifications. Such routine observation uncovers quality problems as they occur and allows for correction before major rework becomes necessary.
5. The principle of single statement. Every time the same piece of data or information is repeated, the odds increase that an inconsistency will occur. The more times an item of information appears in the drawings and/or the specifications, the harder it is to ensure that the impact of a future design change can be fully identified.
For instance, if the same dimension appears on 14 different drawings, it is likely that a future design change will not be caught on at least one of these drawings. This would lead to a design error and potentially a claim by a subcontractor. The best way to avoid this problem is to adopt the principle of single statement; in other words, “Say it once, be sure it is right, and don’t say it again.”
PSMJ has developed our library of interactive, expert-led sessions in response to the specific needs of A/E/C industry firms. Together with on-site training such as PSMJ’s A/E/C Project Management Bootcamp, firms now have the ability to train PMs matching a professional’s need to a platform. PSMJ's newest online learning courses are delivered in an interactive and engaging format to ensure PM's get action-oriented strategies and tactics that they can really use.
You also might be interested in these related blog posts:
10 Things Every Project Manager Must Know
5 Tools Every Project Manager Should Be Using
Are You a Project Manager or Project Admin?
What Are The Traits Of The Best Project Managers?